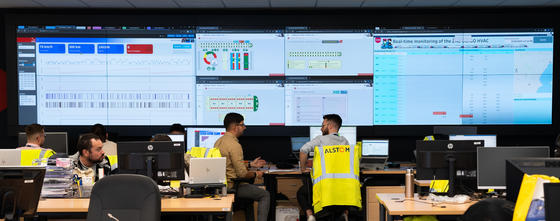
A different and smart approach to maintaining trains

Sometimes a change in working practices can be as significant as a technological leap in bringing savings to Alstom and its customers. A breakthrough on both fronts is changing the way Alstom maintains fleets of trains.
What is Alstom doing to digitalise and optimise maintenance activities across depots?
NA: Traditionally, each maintenance project has a dedicated team based in one depot, with people responsible for planning, engineering, materials, etc. Where there are several similar projects in a region, we have a huge duplication of resources. We are now moving towards the idea of having Maintenance Performance Centres (MPCs) in certain areas, where we group expertise together in one location to serve several fleets – strategic decision-makers at the centre, with teams at the depots focused purely on operations and maintenance.
To set up an MPC, you need a strong IT backbone and a robust maintenance management system, so the MPC team can exploit advanced digital tools for the real-time performance visualisation of the fleets, technical support and work allocation.
Combining these digital technologies with Alstom’s lean ways of working has allowed us to rethink how we optimise rolling stock maintenance. One advantage is that we can quickly integrate new contracts and customers into an MPC, instead of having to recruit a new team of people in a specific location. In an area where there is a lack of competent people in specific disciplines, we can potentially operate remotely from an area where those skills exist; an MPC gives us the flexibility to respond more quickly to customer needs.

Has an MPC already been deployed in Alstom? And, if so, what benefits are the sites seeing?
NA: We are currently setting up the first MPCs, one in Braunschweig, Germany, and another in Ontario, Canada. The Braunschweig MPC is responsible for executing 13 rolling stock maintenance contracts. Currently the Braunschweig team is focused on setting up the structure and the interfaces between project teams and supporting functions in the MPC, and transforming the way of working towards a best-in-class operational model. They have already seen huge improvements in data quality in the maintenance management system and have identified further opportunities for standardisation to improve both team and fleet performance.
Which digital tools, to improve maintenance, are particularly relevant to MPCs?
JW: A key one is Digital Work Instructions, which is Alstom's own proprietary web-based software. It is both a technical publications tool and an interactive electronic technical manual. It is currently deployed on around 35 projects across the world. Each member of the maintenance team receives, via their tablets, not only a list of tasks to do on each shift, but the work instructions on how to perform each task. Also, many tasks require the team to perform further related tasks. With Digital Work Instructions, there is no need to return to the office, they just click on the relevant link and it takes them to that corrective task, alongside a list of parts and personal protective equipment (PPE) needed.


Also, there is enhanced communication between the maintenance team members and the MPC. Our ‘assisted reality’ tool, which is an industrially-secure communication tool, can be used to contact a technical expert, sharing a live video of the train or component. The intermediate level of the solution involves assisted reality smart glasses with integrated voice commands. The expert can share a diagram directly to the worker’s smart glasses and annotate certain areas of the diagram in real-time. The worker then has hands-free advice and visuals for the job they are doing. The advanced level of the solution allows the user to connect devices such as thermal imaging cameras for more detailed specialist advice. During the pandemic, when travel was restricted, on certain projects, we saved around 60% of journeys through this kind of remote support.
Additionally, we are deploying a range of smart tools to improve railway safety. For example, we know that quite a high proportion of safety issues are related to fasteners: nuts, bolts and screws. We have deployed a smart torque solution, which is a combination of wirelessly connected torque wrenches and a software solution. For any given task, the tool knows which torque wrenches are needed and what the torque values are, and sets them up automatically. The software controls the activity, so thereby almost eliminating the possibility of human error. From a customer perspective, it gives traceability, as every action is recorded in the system.


What does Alstom have in store for the next phase of MPC and digitalising maintenance?
NA: There are multiple MPC opportunities identified across all regions where we can bring all this digital innovation into play. We now have the option to build tenders based on the MPC. The two key pilot MPCs in Canada and Germany are under way, and we are currently supporting six other MPC projects around the world. There is a lot on the horizon!
JW: On the digital tool side, we are looking at digitalising underfloor wheel reprofiling machines. The data generated by the wheel lathe is useful as we have to regularly repair and reprofile wheels to maintain a safe and comfortable experience for the passengers and on-board staff. Wheels are a costly aspect of train maintenance and they are also the most safety-critical components, so what we learn will feed into improving operational and safety performance.