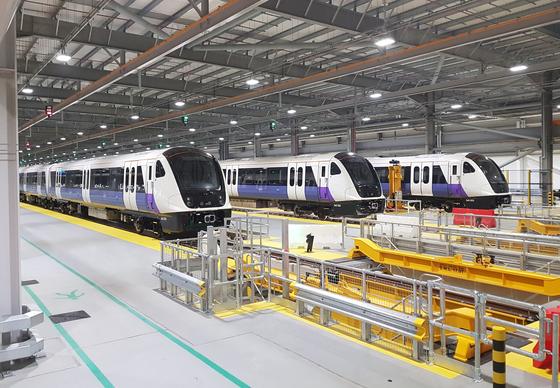
Total cost of ownership: how Alstom’s Adessia commuter trains provide the best value for money
Total cost of ownership: how Alstom’s Adessia commuter trains provide the best value for money

More and more of Alstom’s customers are thinking about Total Cost of Ownership (TCO) before they buy. For rolling stock buyers, the concept is quickly becoming an economical and environmental game-changer. Cost calculations take functional and performance targets over the train’s lifetime into account. This leads to improvements and new developments in train architecture, energy consumption, lightweight and maintenance-friendly train designs, reliable performance, digital solutions and much more - making TCO an enabler for innovation and green mobility.
All of this is especially interesting for commuter trains, as they offer a broad range of operations from inner-city to regional networks, combining the challenge of high passenger volumes and short dwell times with passenger comfort for longer journeys.

Stefan von Mach, Bid Technical Manager for Alstom’s Commuter Rolling Stock Platform, went from collecting trainsets as a boy to studying mechanical engineering in Bordeaux and Glasgow, before obtaining a Masters in Rail Vehicle Engineering from the Technical University of Berlin. Stefan previously spent several years as Chief Engineer at Alstom, developing and homologating Europe’s first Li-Ion battery train. Stefan is also a talented linguist, with several European languages under his belt.
Connect with Stefan on LinkedIn!
What is Total Cost of Ownership?
TCO is a financial estimate used to help operators assess the complete cost of acquiring, operating, and maintaining a product, service or system over its entire lifecycle. TCO takes into account not only upfront costs, such as purchase price, installation and setup, but also ongoing costs, such as energy consumption, maintenance, support, training, operational expenses, and potential downtime.
Why should our customers adopt a “TCO approach”?
Thinking about TCO before making a purchase helps operators to make more informed decisions about their investments. Not only will it reduce costs in the long term; it can help them anticipate and plan infrastructure management and maintenance activities. This approach is particularly important in the railway industry, where the trains run for at least 30 years, meaning that long-term reliability, efficiency, and operational continuity are critical factors in decision-making.
Optimising TCO isn’t just good for the operator - when you optimise the train design with a view to improving energy efficiency and requiring fewer spare parts, it’s also good for the environment.

How does Alstom offer commuter solutions with optimised TCO?
Building a TCO-optimised train calls for energy-efficient propulsion systems, lightweight materials and maintenance-friendly designs, as well as standardisation and a modular approach for more streamlined manufacturing. Alstom has all of these capabilities, as demonstrated by our new, highly standardised product platform, Adessia™. Adessia commuter trains are composed of Alstom’s state-of-the-art subsystems, all of which undergo constant optimisation and can be customised as required. This allows us to offer the very latest energy efficiency technologies, such as our lightweight Flexx Eco™ bogie, energy-efficient HVAC systems, traction heat recovery technologies, digital solutions, and more.

Working with experts all over the world, we use sophisticated optimisation tools, simulations and algorithms to offer TCO-optimised trains to our customers. Alstom backs up all of its TCO optimisation calculations with guaranteed cost savings for our business partners.
But Alstom is not just a manufacturer; we are the market leader in rail services, and operate and maintain fleets around the world, including commuter train fleets. We take care of all aspects of train operations, including train drivers and crew, dispatching, and customer service, and maintain the fleet and the entire system including signalling, railway infrastructure, stations and maintenance facilities. Our operations and maintenance experience gives us much greater insight into how our trains perform, and allows us to close the design loop with the feedback from maintenance to continuously optimise our solutions for TCO.

Can you give us some examples of the benefits of TCO for commuter rolling stock purchasers?
TCO optimisation, in combination with new technologies, can be a real game-changer for operators. One of the clearest examples of this is battery technology. Batteries represent a real revolution in terms of TCO. In addition to offering lower operating and maintenance costs in comparison to diesel propulsion systems, electric traction systems (including batteries) help operators meet sustainability goals: their high efficiency helps to reduce energy consumption, resulting in lower CO2 emissions. Even taking diesel and electricity price fluctuations and national differences in electricity price into account, fleet owners and decision-makers are finally starting to accept battery operation as a realistic, cost-effective alternative to diesel.
The DART Commuter Network in Dublin, Ireland, is a great example of how train optimisation can lead to a winning bid! Reducing energy consumption was a major objective for this project. To achieve this, we replaced the conventional configuration of the cars with an articulated “deported knee” configuration. This allowed us to continue using conventional bogies, which are lighter and used in fewer numbers, as well as providing superior performance. This led to a significant reduction of the weight and a 10-15% reduction in TCO.


Finally, our Aventra™ commuter train fleets operating in the United Kingdom demonstrate how TCO can be optimised to reduce maintenance costs, increase availability and enhance sustainability. The trains were designed with maintenance in mind: as well as being equipped with state-of-the-art subsystems and smart stabling to ensure low energy consumption, we integrated the latest maintenance technologies, such as an advanced fleet monitoring system, and Alstom’s automatic vehicle inspection system. This has allowed major component overhauls to be extended by up to 50% compared to the previous generation of rolling stock, reducing total asset life costs and the impact of overhauls on vehicle downtime. It also resulted in significantly less raw material processed, manufactured and transported for maintenance, bringing major improvements to the sustainability of rolling stock over their full life.
What’s the best way for commuter solutions purchasers to adopt a TCO approach?
It’s all about communication! At Alstom, we are always happy to be in transparent dialogue with our customers and business partners on tender preparation. We propose to our stakeholders to focus on functional requirements in their specifications, rather than giving in-depth technical descriptions, which only closes the door to eventual optimisation down the line. We always recommend using business models that take the complete lifecycle cost into account.
There are many other steps operators can take to ensure TCO-optimised trains in their tenders. These include clearly defining expectations, implementing performance-based contracts, and requesting comprehensive lifecycle cost assessments right from the tender stage. Benchmarking proposals against industry best practices is a good way to assess the efficiency and cost-effectiveness of the solutions being proposed.
Finally, building long-term partnerships with suppliers fosters ongoing developments and allows continuous optimisation of entire transport eco-systems to achieve the best TCO balance.