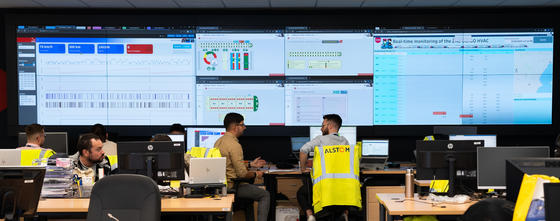
Ein neuartiger und smarter Ansatz für die Instandhaltung von Zügen
Ein neuartiger und smarter Ansatz für die Instandhaltung von Zügen

Manchmal kann eine Änderung der Arbeitsabläufe ebenso bedeutend sein wie ein technologischer Sprung, um Alstom und seinen Kunden Einsparungen zu verschaffen. Ein Durchbruch an beiden Fronten verändert die Art und Weise, wie Alstom Zugflotten instand hält.
Was unternimmt Alstom, um die Wartungstätigkeiten in den einzelnen Depots zu optimieren?
NA: In der Regel gibt es für jedes Wartungsprojekt ein eigenes Team in einem Depot, das für Planung, Technik, Material usw. zuständig ist. Wenn es in einer Region mehrere ähnliche Projekte gibt, haben wir eine enorme Doppelung der Ressourcen. Wir gehen jetzt dazu über, in bestimmten Gebieten Maintenance Performance Centres (MPCs) einzurichten, in denen wir unser Fachwissen an einem Ort bündeln, um mehrere Flotten zu betreuen - mit strategischen Entscheidungsträgern im Zentrum und Teams in den Depots, die sich ausschließlich auf Betrieb und Wartung konzentrieren.
Um ein MPC einzurichten, braucht man ein starkes IT-Fundament und ein robustes Instandhaltungsmanagementsystem, damit das MPC-Team moderne digitale Tools für die Echtzeit-Visualisierung der Flottenleistung, den technischen Support und die Arbeitszuweisung nutzen kann. Die Kombination dieser digitalen Technologien mit der schlanken Arbeitsweise von Alstom hat es uns ermöglicht, die Optimierung der Fahrzeuginstandhaltung neu zu konzipieren. Ein Vorteil ist, dass wir neue Verträge und Kunden schnell in ein MPC integrieren können, anstatt ein neues Team von Mitarbeitenden an einem bestimmten Ort aufbauen zu müssen. In einem Gebiet, in dem es an kompetenten Mitarbeitenden in bestimmten Disziplinen fehlt, können wir möglicherweise aus der Ferne von einem Standort aus operieren, an dem diese Fähigkeiten vorhanden sind; ein MPC gibt uns die Flexibilität, schneller auf Kundenbedürfnisse zu reagieren.

Wurde ein MPC bereits bei Alstom eingesetzt? Und wenn ja, welche Vorteile ergeben sich für die Standorte?
NA: Wir richten derzeit die ersten MPCs ein, eines in Braunschweig und ein weiteres in Ontario, Kanada. Das MPC in Braunschweig ist für die Ausführung von 13 Instandhaltungsverträgen für Fahrzeuge verantwortlich. Derzeit konzentriert sich das Braunschweiger Team darauf, die Struktur und die Schnittstellen zwischen den Projektteams und den unterstützenden Funktionen im MPC einzurichten und die Arbeitsweise in Richtung eines Best-in-Class-Betriebsmodells zu verändern. Sie haben bereits enorme Verbesserungen der Datenqualität im Instandhaltungsmanagementsystem erreicht und weitere Möglichkeiten zur Standardisierung identifiziert, um sowohl die Team- als auch die Flottenleistung zu verbessern.
Welche digitalen Werkzeuge zur Verbesserung der Instandhaltung sind für MPCs besonders relevant?
JW: Eines der wichtigsten ist die Alstom-eigene webbasierte Software „Digital Work Instructions“. Sie ist sowohl ein Werkzeug für technische Veröffentlichungen als auch ein interaktives elektronisches technisches Handbuch. Sie wird derzeit bei etwa 35 Projekten in der ganzen Welt eingesetzt. Jedes Mitglied des Wartungsteams erhält über seine Tablets nicht nur eine Liste der in jeder Schicht zu erledigenden Aufgaben, sondern auch die Arbeitsanweisungen für deren Durchführung. Außerdem erfordern viele Aufgaben, dass das Team weitere damit verbundene Tätigkeiten ausführt. Mit den digitalen Arbeitsanweisungen müssen die Teammitglieder nicht mehr ins Büro zurückkehren, sondern klicken einfach auf den entsprechenden Link, der sie zu der entsprechenden Aufgabe führt, zusammen mit einer Liste der benötigten Teile und persönlichen Schutzausrüstung (PSA).


Auch die Kommunikation zwischen den Mitgliedern des Wartungsteams und dem MPC wird verbessert. Unser „Assisted Reality“-Tool, ein industrietaugliches Kommunikationstool, kann verwendet werden, um einen technischen Experten oder eine Expertin zu kontaktieren und ein Live-Video des Zuges oder der Komponente zu teilen. Die Zwischenstufe der Lösung besteht aus Assisted Reality Smart Glasses mit integrierter Sprachsteuerung. Der Experte oder die Expertin kann ein Diagramm direkt auf die Smart Glasses übertragen und bestimmte Bereiche des Diagramms in Echtzeit mit Anmerkungen versehen. Die Mitarbeitenden haben dann eine freihändige Beratung und visuelle Unterstützung für die ausgeführte Arbeit. Die fortgeschrittene Version der Lösung ermöglicht es, Geräte wie Wärmebildkameras anzuschließen, um eine detailliertere fachliche Beratung zu erhalten. Während der Pandemie, als die Reisemöglichkeiten eingeschränkt waren, konnten wir bei bestimmten Projekten durch diese Art der Fernunterstützung rund 60 % der Reisen einsparen.
Darüber hinaus setzen wir eine Reihe von intelligenten Instrumenten zur Verbesserung der Eisenbahnsicherheit ein. Wir wissen zum Beispiel, dass ein recht hoher Anteil von Sicherheitsthemen mit Verbindungselementen zusammenhängt: Muttern, Bolzen und Schrauben. Wir haben eine intelligente Drehmomentlösung eingeführt, die aus einer Kombination von drahtlos verbundenen Drehmomentschlüsseln und einer Softwarelösung besteht. Das Werkzeug weiß, welche Drehmomentschlüssel für eine bestimmte Aufgabe benötigt werden und welche Drehmomentwerte erforderlich sind, und stellt sie automatisch ein. Die Software steuert den Vorgang, so dass die Möglichkeit menschlicher Fehler nahezu ausgeschlossen ist. Aus Sicht des Kunden ist die Rückverfolgbarkeit gegeben, da jede Aktion im System aufgezeichnet wird.


Was hat Alstom für die nächste Phase der MPCs und der Digitalisierung der Instandhaltung geplant?
NA: Es wurden mehrere MPC-Möglichkeiten in allen Regionen identifiziert, bei denen wir all diese digitalen Innovationen ins Spiel bringen können. Wir haben jetzt die Möglichkeit, Ausschreibungen auf der Grundlage der MPCs zu erstellen. Die beiden wichtigsten MPC-Pilotprojekte in Kanada und Deutschland sind bereits angelaufen, und wir unterstützen derzeit sechs weitere MPC-Projekte in der ganzen Welt. Es gibt viel zu tun!
JW: Auf der Seite der digitalen Werkzeuge befassen wir uns mit der Digitalisierung von Maschinen zur Unterflur-Rad-Reprofilierung. Die von der Raddrehbank erzeugten Daten sind nützlich, da wir regelmäßig Räder reparieren und reprofilieren müssen, um ein sicheres und komfortables Reiseerlebnis für die Fahrgäste und das Zugpersonal zu gewährleisten. Die Räder sind ein kostspieliger Aspekt der Zugwartung und gleichzeitig die sicherheitskritischsten Komponenten, so dass die gewonnenen Erkenntnisse in die Verbesserung der Betriebs- und Sicherheitsleistung einfließen werden.